金属(アルミ)での加工検証
ブログの更新までなかなか手が回らず,久しぶりの投稿になってしまいました.ソフトウェアの機能追加や修正をデイリーで行っていました.その間にも展示会に参加したりしていました.おかげさまで弊社のソフトウェアに興味を持っていただけるお客様がだんだんと増え始めてきました.また,お客様からの要望を色々と聞けば聞くほど,まだまだやるべきことは多いと感じる日々です.一つずつ対応していきますので.
さて,今日は弊社ソフトウェアが実際に金属を加工できるまでのものに仕上がっているのかということを検証するために,被削材にアルミを使って加工してみました.(これまではケミカルウッドばかりを加工していたので,実際の加工現場に使えるのかという疑問にお答えします.)
加工する形状はおなじみの3DスキャナでSTLモデルを作成したシーサーです.
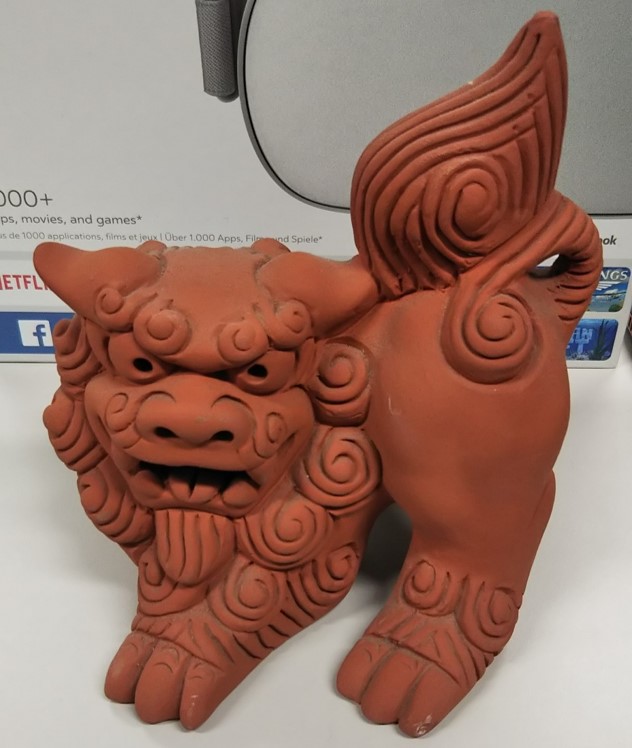
実際に3Dスキャンから弊社ソフトウェアでのNCプログラムの生成,NC工作機械での加工の様子をYouTubeにアップしています.詳細はこちらのリンクを見てください. さて,加工した結果はこうなりました.
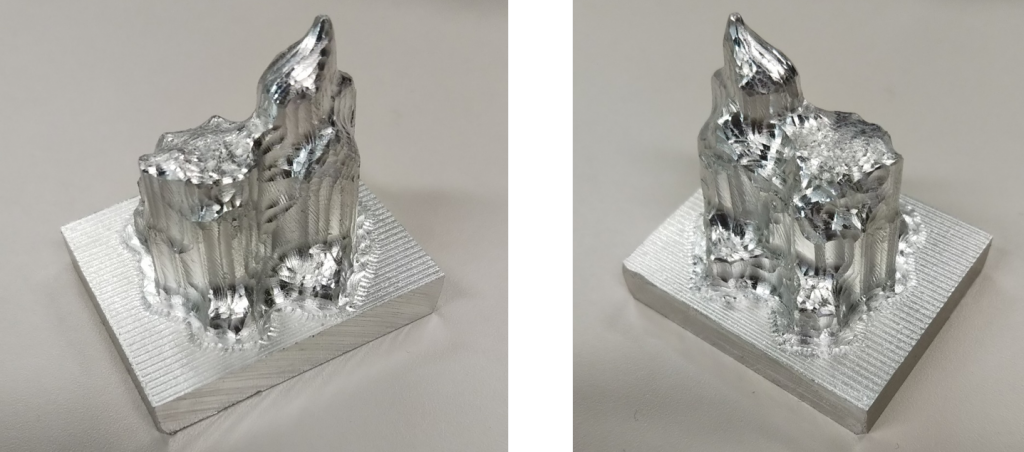
ひとまずお手軽にモデリングからNCプログラムの生成ができて,アルミでも加工ができたんじゃないかと思います.ただ,今回は3軸加工の走査線加工しか行っていませんので,当然シーサーの細かい部分までは加工できていませんね.また,今回加工条件としては,残り代0.5mmでスクエアエンドミルで荒加工した後に,ボールエンドミルで仕上げ加工をしましたが,もう少し残り代を大きくして荒加工をしてもよかったかなと思っています.やはり,最適な加工条件を決定するのって非常に難しいです.まぁ,最初の検証としては及第点かなと思います.展示会で展示できるレベルかなと思いますので,次回展示会で出展する際に展示します.
さてさて,次に最近中高年に再ブレークしているミニ四駆のボディなんかを加工できればおもしろいんじゃないかと思い,息子と一緒に実際にミニ四駆を購入して,ボディを3Dスキャンしてみて加工に挑戦しました.
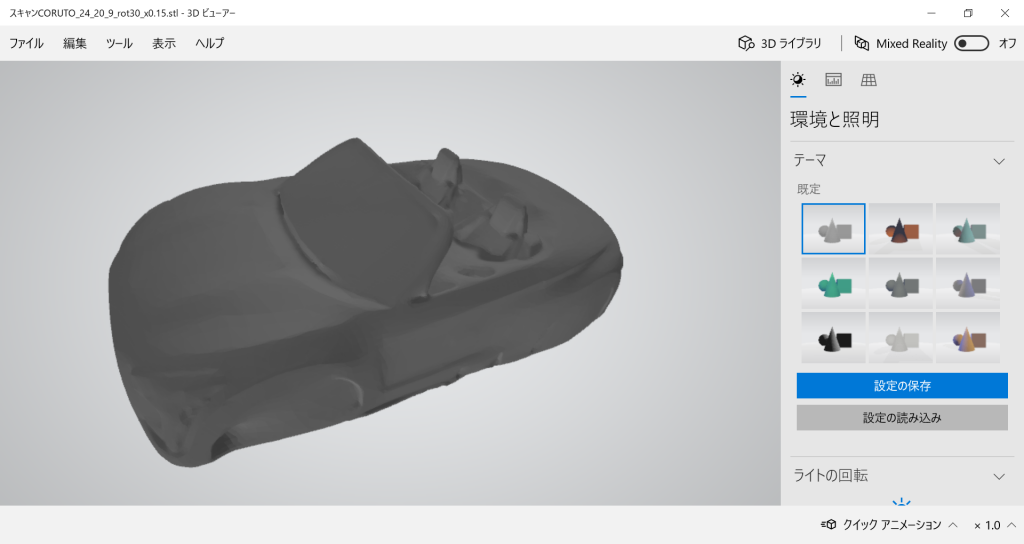
モデルは少し粗いですが,フロントや運転席が表現できています.いざ加工してみました.その結果...
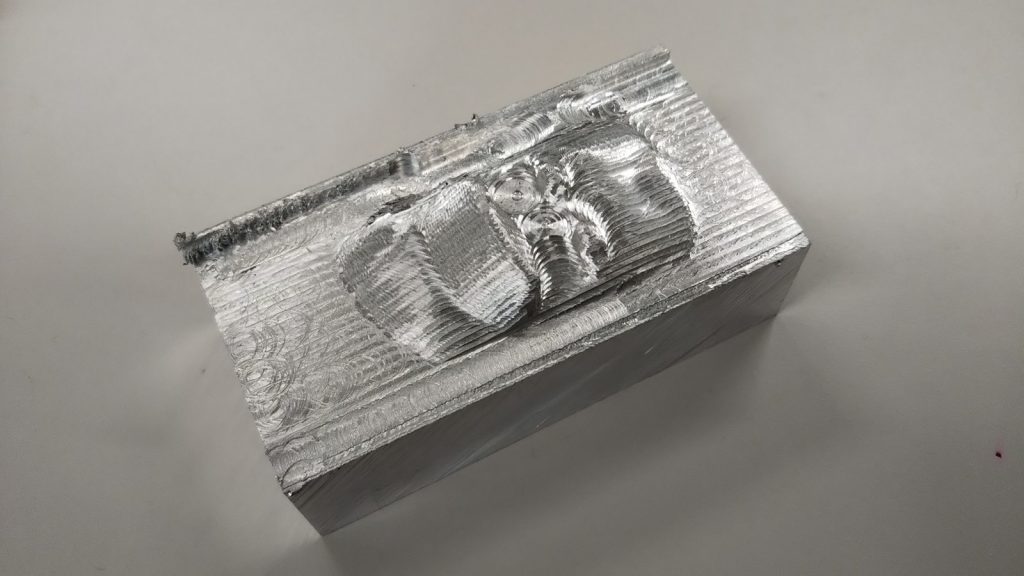
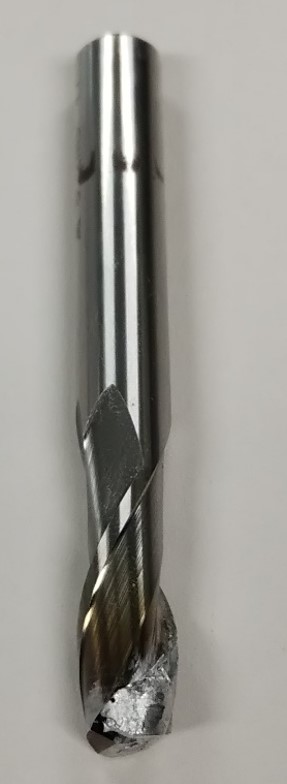
失敗です.切りくずが工具に凝着して,加工を断念しました.今回加工条件としては,工具径8mm,半径方向切込み1mm,軸方向切込み2mmで送り速度F800で加工していましたが,軸方向切込みが大きかったかもしれません.あと,失敗して気づきましたが,現状の走査線加工のパスだと,奥側を加工する際(今回凝着を起こした箇所)に,切りくずの逃げ場所がなくなりますね.たまたまシーサーのモデルでは被削材いっぱいいっぱいにモデルが配置されていたので,大丈夫でしたが,モデルと被削材の端の間が大きい場合に,工具が八方ふさがりになってしまいます.これはどうにか対応しないとまずいですね.
ということで,ちょうどGWの宿題がまた増えました.急いで対応します!!